THE
GENERATOR
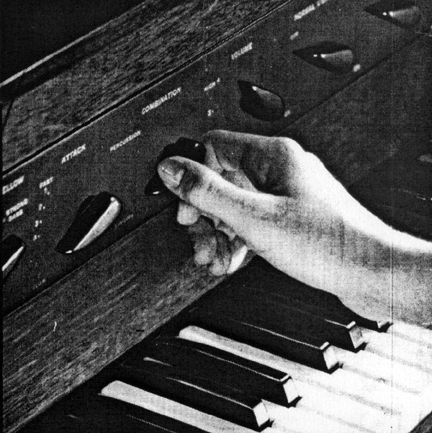
The "brain" of the instrument
The massive "Generator"
consists of the control box in the front, and channels 1 through
9 in the rear. All the audio processing in the Novachord is performed
in the generator.
The Control Box
houses the controls for the instrument as well as all the passive
audio processing circuits including the 5 resonators.
Channels 1 - 9
house the active vacuum tube circuits. There are 12 oscillators,
60 frequency dividers, 60 band pass filters, 72 VCA's, a pre amp
and a hex-vibrati in the generator. There are a total of 146 tubes
in the generator.
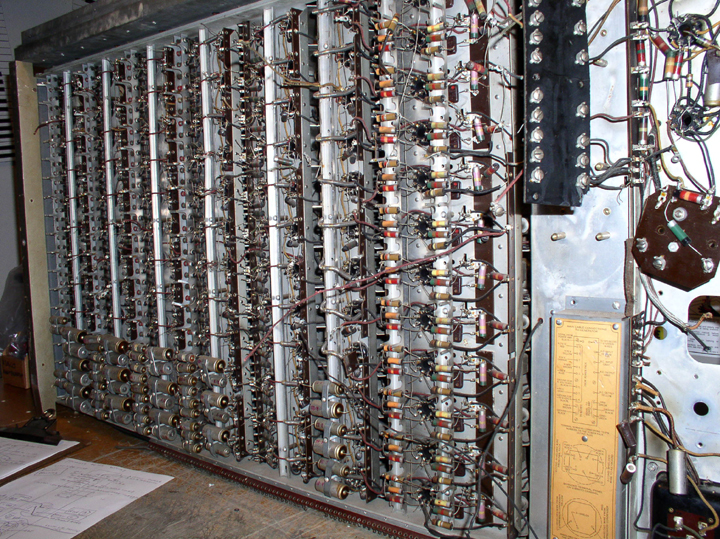
Stripping the underside of the generator.
The
Control Box

The Control Panel
before restoration. The one saving grace about
this particular Novachord is that the front panel is in good condition.

The Control Box internals
before restoration - The rear section (shown above) contains
the 18 channel passive mixer with it's Rube Goldberg mechanical
keyboard volume balancer.
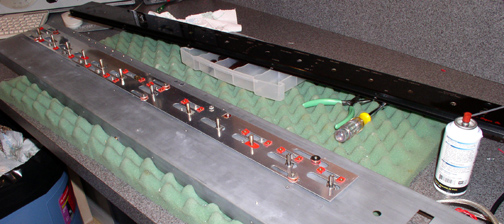
The preset mechanism
- The Combination lever engages the 2 preset sounds of the Novachord.
A cam that slides underneath the front panel sets all the controls
to either the "Percussion" preset or the "Singing"
preset. The "Percussion" preset is very close to a piano
sound. The "Singing" preset is somewhat organ like.
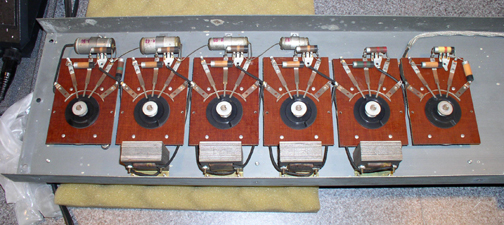
The Resonator Filter Bank
before restoration - The front section of control box
(the control panel) houses the filters and the controls for the
instrument. A combination of rotary switches sets the tone of
the Novachord. From left to right: 1 low pass, 3 band pass, 1
high pass and 1 bypass.
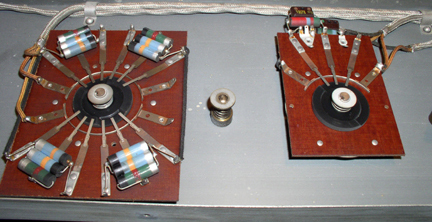
The Attack Control - On
the left half of the above photo is the attack control. A seven
position switch that actually adjusts the attack, decay and sustain
of all 72 notes. The release is engaged by a foot pedal. This
is one of the many features of the Novachord that place it in
the domain of the synthesizer. And you thought the ADSR was invented
in the 60's - not true. The control on the right is the volume
control.
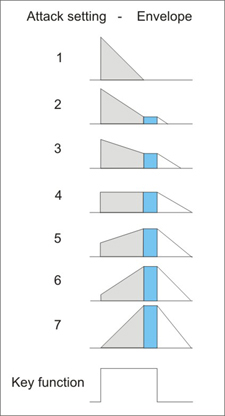
The Operation of the Envelope
Generators is shown in the diagram above. The gray shaded
areas are the attack and decay functions. The blue shaded area
is the sustain voltage as the key is held down. The white areas
are the release function engaged by the foot pedal after the key
has been released. The times are not variable, but the levels
are. Somewhat limited, but amazing for a pre-WW2 synthesizer.
Setting 1 is for percussive type envelopes. Setting 3 looks like
a typical synthesizer ADSR setting. Setting 4, without the release
function is an organ envelope. Setting 7 would be great for string
simulation. Please note that the release also works on setting
1 if the key is released soon enough.
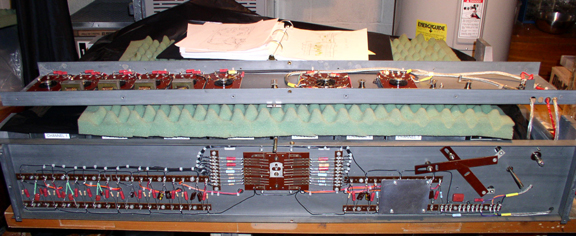
The Control Box after restoration
- I ended up replacing all the passive components.
Restoration
of the Individual Generator Channels 1 to 9
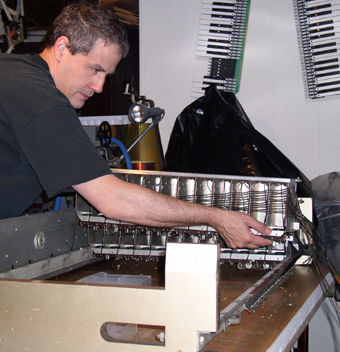
Disassembly of the Generator
- Some kind of madman pulling out channel 2.
The 9 generator
channels were tackled in descending order:
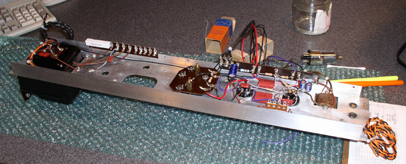
Channel
9 after restoration - The
Preamplifier - gone are the nasty capacitors.
There was a massive PCB oil filled capacitor in the center of
this channel. But I suspect the real culprits of the contamination
were the 2 "black tar" capacitors mounted alongside
of the oil capacitor. The black goo
that was leaking out of them was incredibly nasty. It had an awful
smell and a very low boiling point. If a soldering iron got near
the stuff, it started bubbling like crazy and emitting these nasty
fumes. I never encountered anything like this, but I knew I didn't
want it in my house. To clean the channel properly, I had to strip
it to the chassis. While I was cleaning the "tar of doom"
off of the chassis, I noticed it had one good quality - It polished
the chassis to an almost mirror like shine. So, I polished the
whole chassis with descending grades of steel wool. It looked
and smelled much better. The preamplifier is a simple circuit
compared to the rest of the instrument. So I knew at that point,
I had a long long road ahead of me.
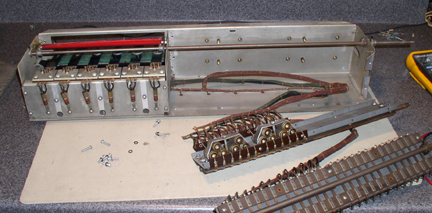
Channel 8 before restoration
- There are 36 capacitors beneath the 3 X 12 pole switches.
The wiring harnesses leading to the reeds and oscillators were
composed of cotton covered wire that wreaked of PCBs. They all
needed to be replaced.
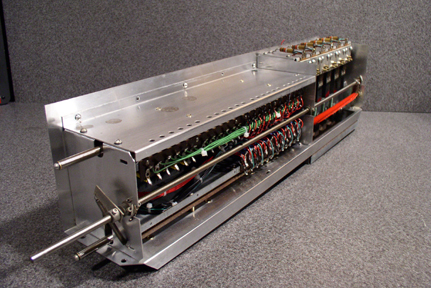
Channel
8 after restoration - The
Hex Vibrati -
the 6 mechanical reeds in the back housing are always wiggling.They
are engaged through 3, 12 pole switches to each oscillator so
that when you play a chord - each note has a different vibrato
rate. Individual LFO modulation of each note - nice. The red bar
starts the reeds moving manually by a lever on the front panel.
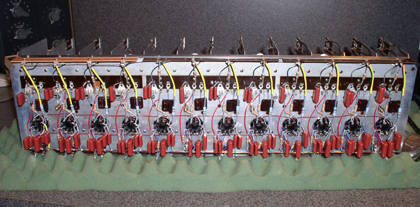
Channel 7 restored
- This is the underside of the twelve oscillator circuits comprising
the top octave tone generators.
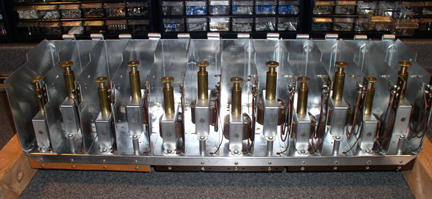
This is the top of Channel
7 after restoration - the custom transformers have adjustable
cores that are used to fine tune the instrument. Each compartment
in channel 7 houses a transformer, a tube and a coarse tuning
capacitor.
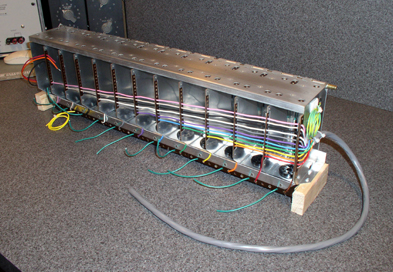
Channel
6 after restoration - This
channel houses the twelve VCA's for the top octave. The loomed
wire supplies the signals from the individual envelope generators
in the keyboard. At this pont, I am
planning to eliminate the spring connectors and use circular multi-pin
AMP connectors instead.
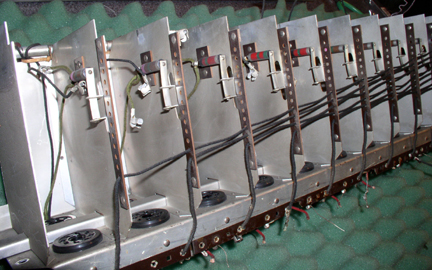
Channel 5 before restoration.
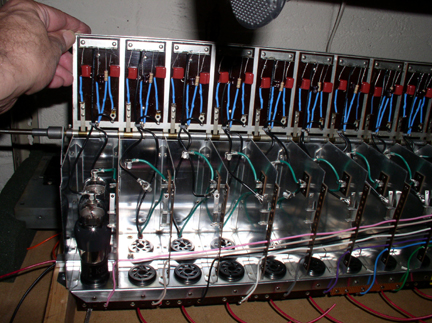
Channel 5 after restoration
- Each compartment houses a frequency divider tube, a VCA tube
and a passive band pass filter under the lid. The hinge of the
compartment has a switch mechanism that reduces the bandwidth
of each band pass filter for the "mellow" setting. The
first compartment has a pair of tubes in it for show. There are
5 channels like this one in the generator, each with 12 compartments,
for a total of 60 circuits. Fun fun fun!
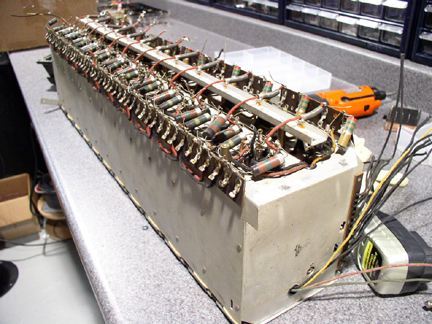
Channel 4 before restoration
- the capacitors and the large resistor mounting bar have been
removed.

Channel 4 during restoration
- Here are some of the custom PCB's I made to replace the smashed
terminal strips.
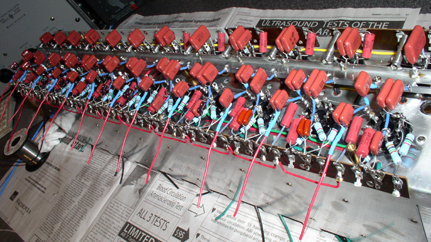
Channel 4 after restoration
- This is the underside showing the polypropylene film caps and
the metal film resistors. Many of the capacitors had to be doubled
up to get the correct value specified by the factory. Also, due
to tolerance limitations, all values and combinations of values
had to be selected and verified on a digital capacitance meter.
The 5 divider/vca channels end up using about 150 capacitors each.
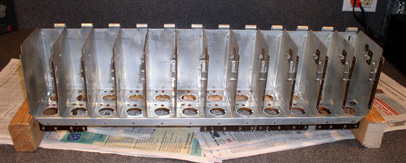
Channel 3 - during restoration
- This is the chassis of channel 3 before polishing.
The Novachord Restoration Project involves removing all the components,
all the wiring, removing all the tube sockets, cleaning and polishing
the chassis, installing the reconditioned tube sockets, installing
new wiring, resistors and capacitors.
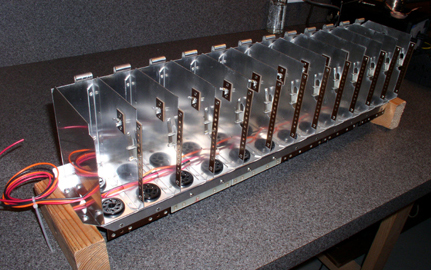
Why go this far? -
The primary reason I went so far with the cleaning, polishing
and rewiring was to protect my family's health.
The pre amp and the power amp did have several leaking oil caps
containing PCB's. The entire inside of the instrument was covered
with this black precipitate that had a very unusual smell. My
gut and my nose told me not to let this thing heat up for extended
periods in my house without a total decontamination. To be frank
- I didn't want to take a chance with other peoples health. Plus
it looks great.
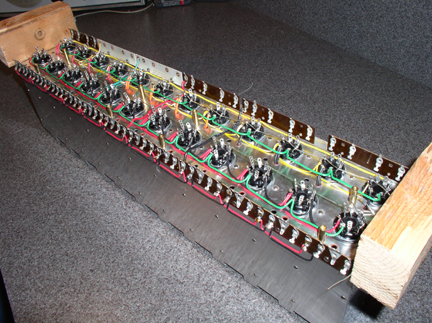
Channel 3 after polishing
and wiring - A large amount of elbow grease was required.
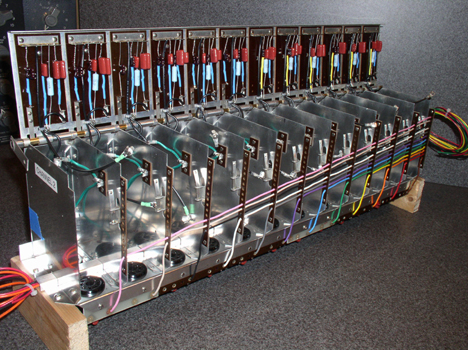
Channel 2 After restoration
- A light at the end of the tunnel.
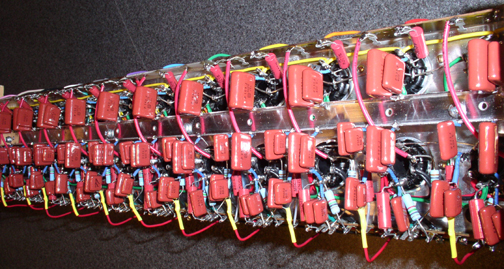
Channel 2 after restoration
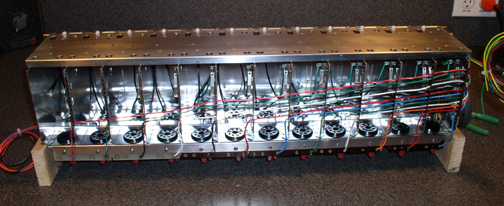
Channel 1 after restoration
- The next step is to paint the generator frame and assemble the
generator.
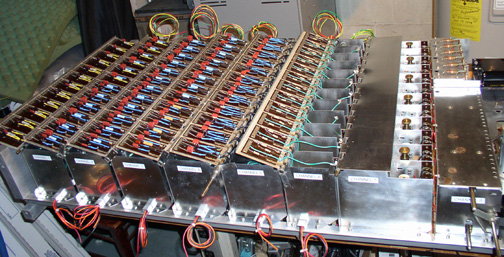
Assembling the Generator
- The compartment lids are open.
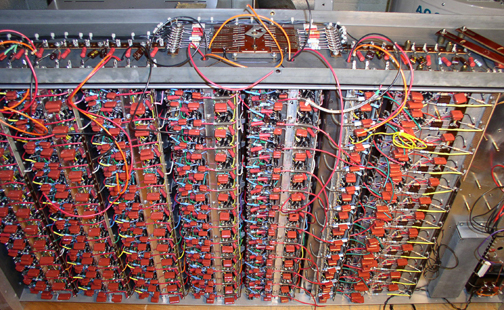
The underside of the Generator
during assembly - The worst is over.
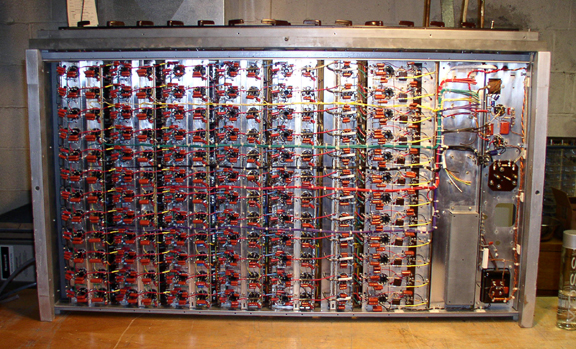
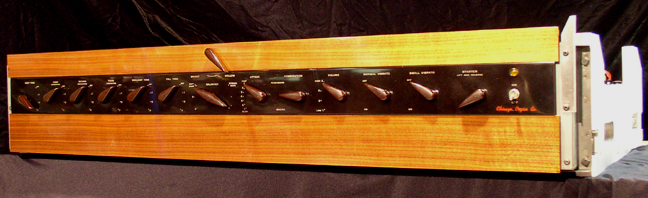
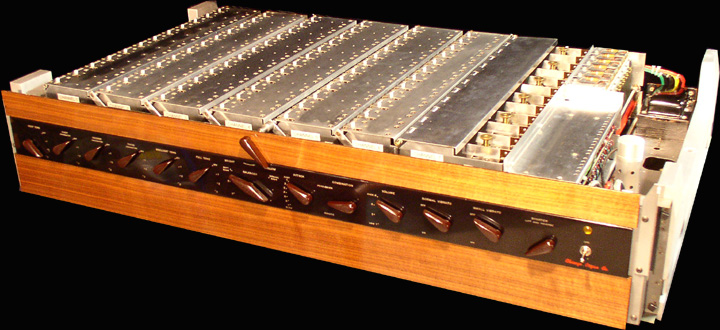
The Generator after restoration
- All ready to go.
THE
KEYBOARD
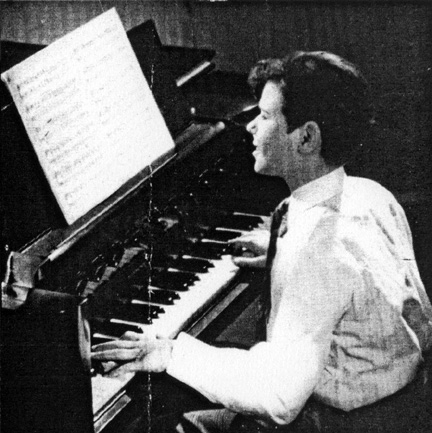
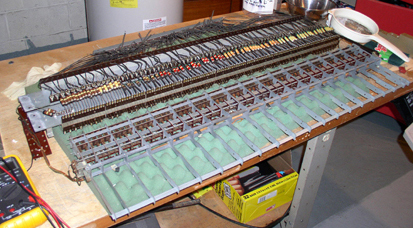
Keyboard Assembly
- Here's a shot of the keyboard frame assembly during contact
cleaning and restoration. Like the generator, it has many compartments.
They house the multiple contacts per key and the cam that engages
the release function of all 72 envelope generators. The engineering
is quite intricate and advanced for 1938. It sometimes reminds
me of working on my old V. W.- Porsche.
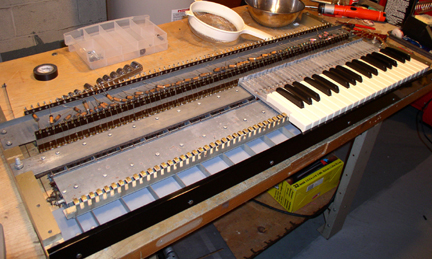
Assembling the keyboard mechanicals.
The envelope generators were in the rear section.
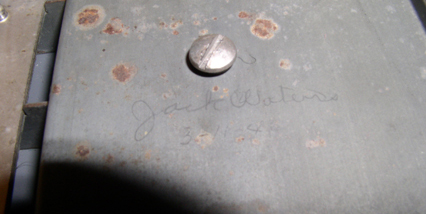
A message
from the past - Jack Waters
finished the keyboard assembly on 3 /11/ 1940
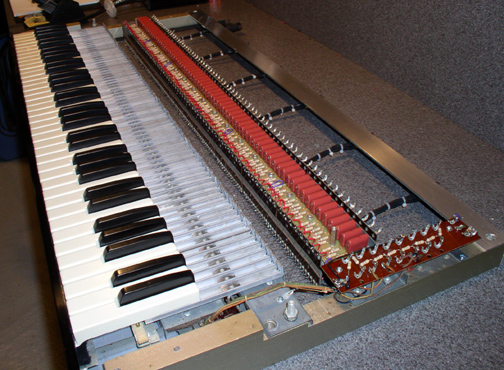
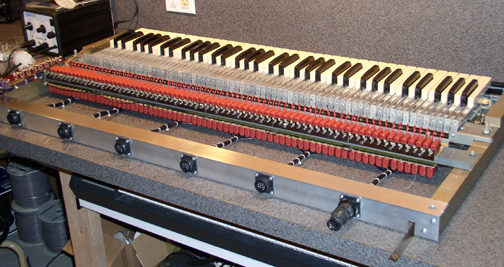
The Keyboard Assembly after
restoration - I used the Altium PCB program to design
custom circuit boards for the key circuit. 12 PCB's were mounted
on top and bottom of the front component rail. The rear component
rail, as well as the spring connector assembly were removed. 7
AMP connectors were installed, 1 for each octave and 1 for the
keyboard power to facilitate transportation (ha ha). Note the
144 capacitors.
THE
POWER SUPPLY
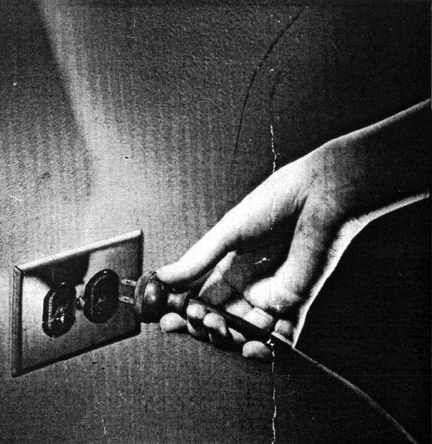
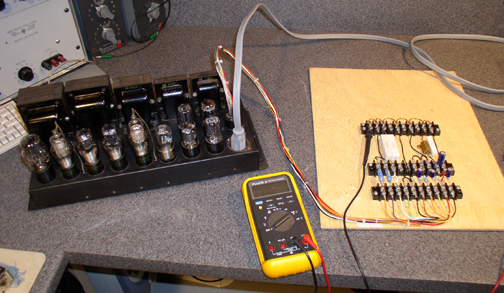
The Dummy Load -
A fellow Novanaut, Stephen Kamm gave me his recipe for a dummy
load, so I can check the voltages coming off the power supply
before I hook it up.
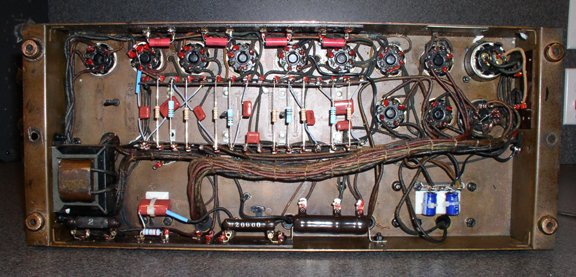
The underside of the power
supply - The passive components were replaced at the
start of the NRP. All the cotton covered wiring needed to be replaced
to eliminate the contamination.
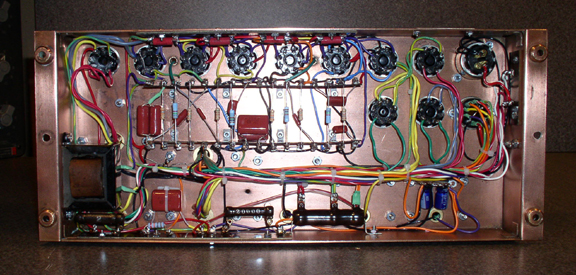
Underneath the rebuilt power
supply - Just in case you haven't figured it out yet,
this was a massive project in itself.
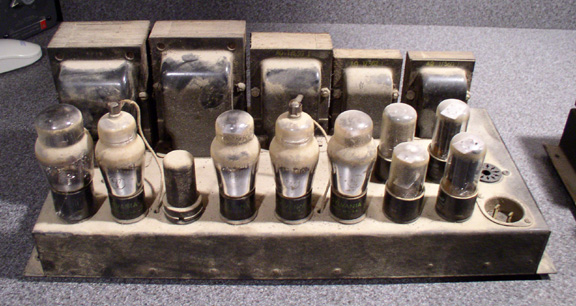
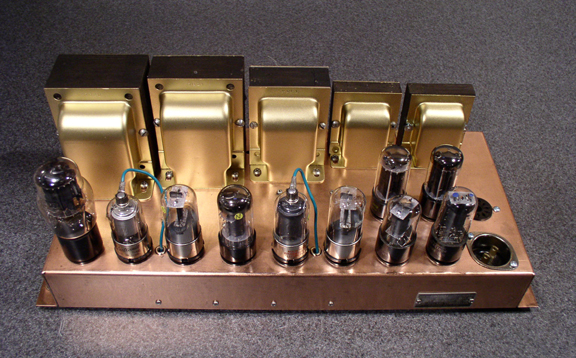
The rebuilt power supply
- The outside was polished with steel wool and clear coated. The
transformer bells were stripped and painted.
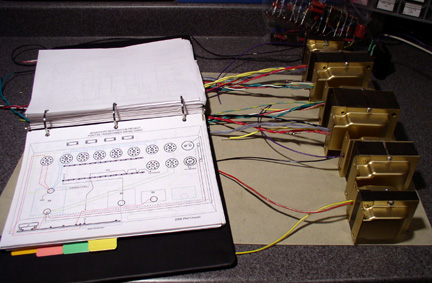
Extensive documentation
was necessary as the power supply was taken apart to be able to
wire it up correctly again. Also the transformers had to have
their bells removed and reconditioned. The contaminated wire was
removed at the winding connections and replaced with high temp
wire. Insane, I know.
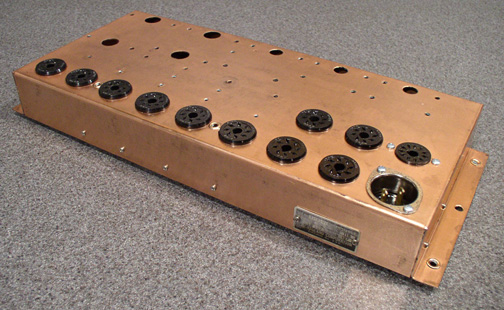
The Copper Plated Chassis
- Huh? Yes, it's true. It was very difficult to remove the rubberized
paint from the chassis to expose the copper finish. The plating
was quite thick however. The nameplate says it was made by the
Rauland Corp. Many early Hammond amplifiers were made by Rauland
and Webster. In my opinion, Rauland made a better instrument.
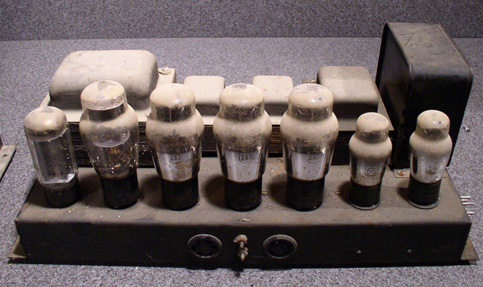
The Field Coil Power Amplifier
- These are highly regarded in tube amp circles, but the two 12"
speakers just can't cut the high end. Here it is before a cleanup.
This amplifier was also made by Rauland.
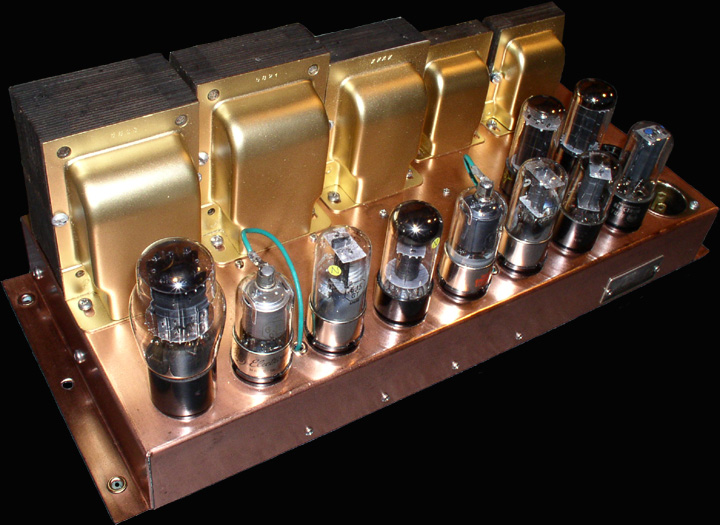
THE
CABINET
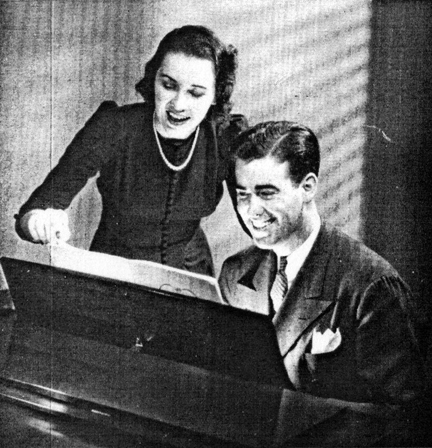

Sick Puppy! - Here
is the cabinet with the keyboard and generator removed. That is
not a Novachord bench. Hope to find one one day.
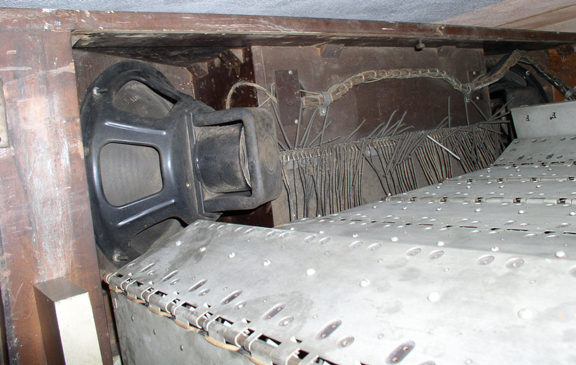
A peek at the speakers
- Pictured in this photo are the 2 Jensen field coil speakers,
wiring harness and the 72 spring connectors. This photo was taken
early on before disassembly. The boxes in the lower area of this
photo are the lids of the generator as it stands upright in the
service position.
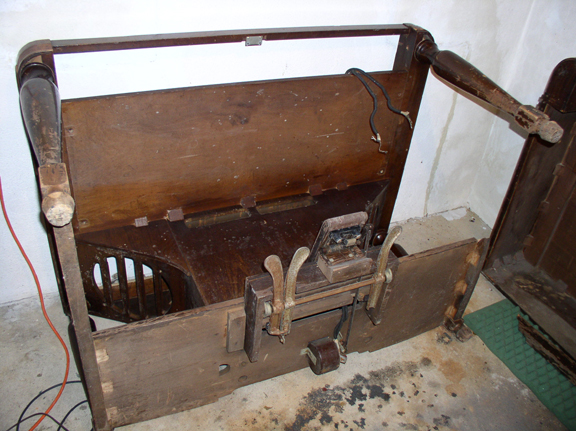
The underside of the lower
cabinet - You can see the sustain pedals and the expression
pedal. The expression pedal has a connecting rod that travels
to the large variable capacitor that sits underneath the power
amplifier shelf. Large shielded cables connect this capacitor
to the preamplifier in the generator.
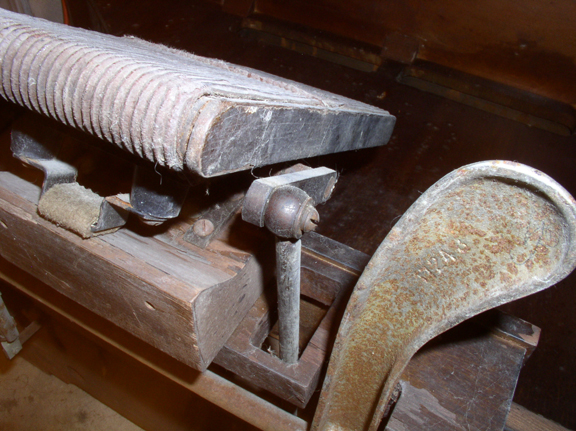
Aye, she looks like she's
been at sea! - Extensive restoration was required in
the lower sections due to moisture damage.
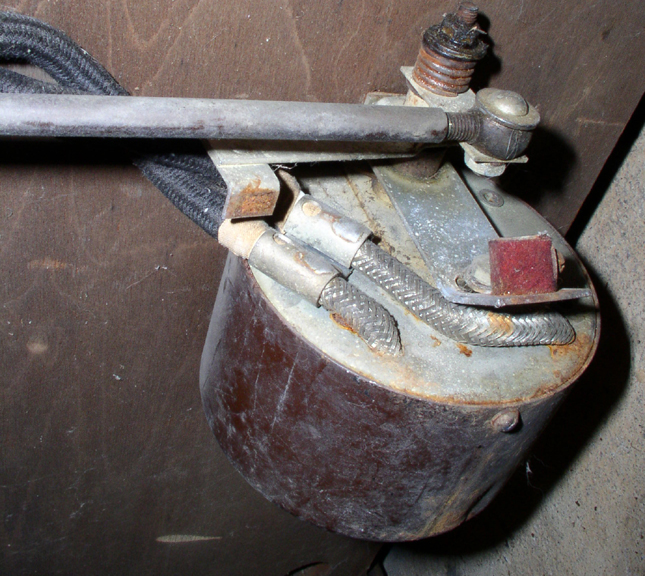
The expression pedal connecting
rod - has a ingenious self adjusting mechanism.
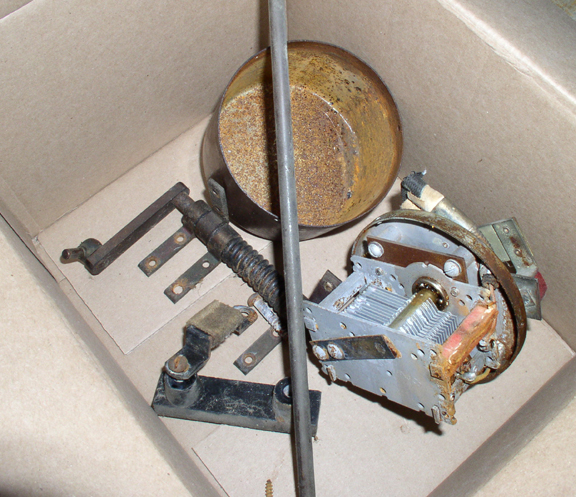
Specialized parts
- ball bearings and gears drive the variable capacitor inside
the shielded housing.
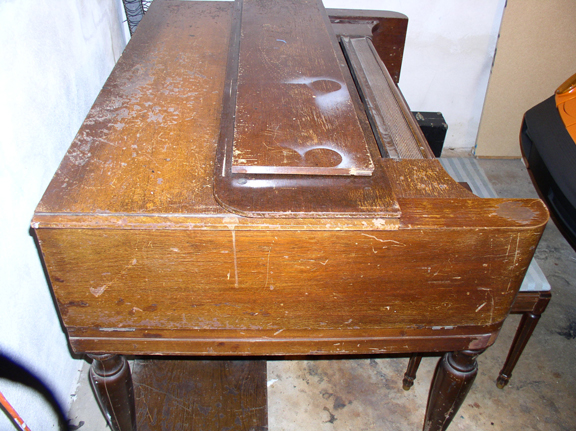
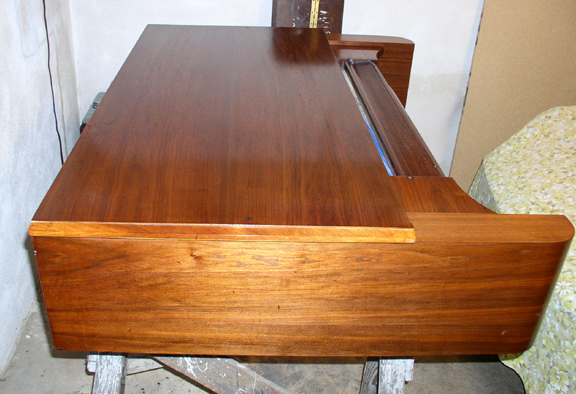
The generator cover - before
and after! - Amazingly, Most of the cigarette burns,
Cocktail rings and scars sanded right out. Nearly all of the veneer
was intact.
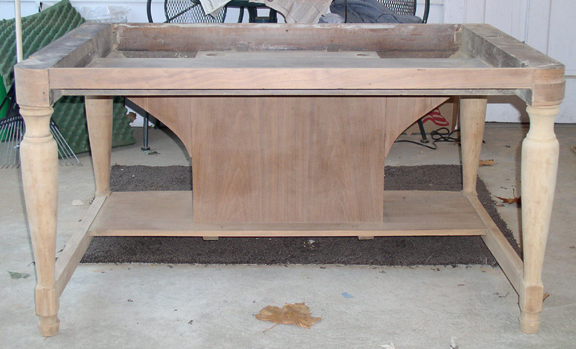
After sanding -
I discovered that the legs and the braces are made of a softer
and lighter hardwood. These sections required staining so as to
match the mahogany veneer on the other sections of the Novachord.
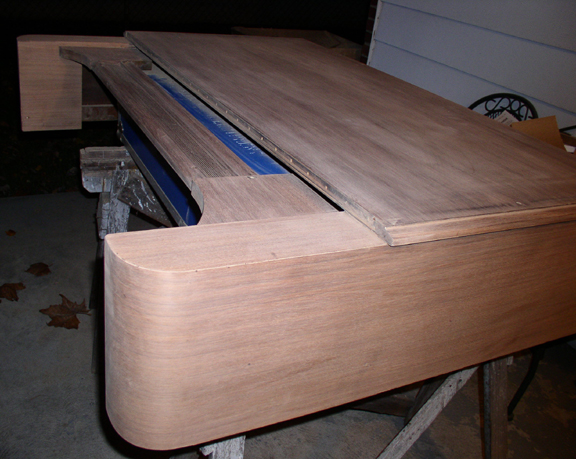
Sanding past the stain
- The veneer was quite thick, so it was possible to sand off the
stain without burning through the veneer. This took a incredible
amount of hand sanding.
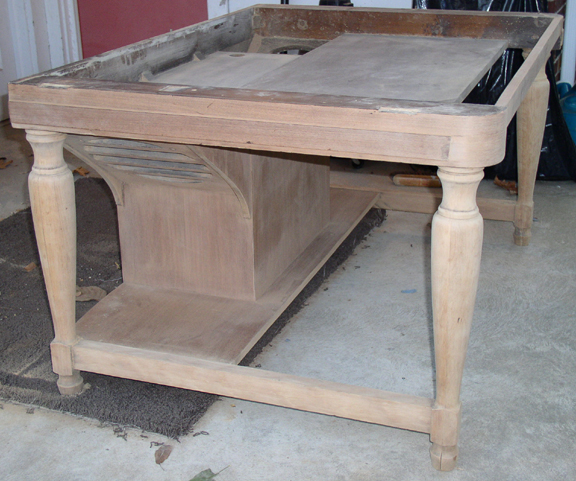
The speaker grilles
- These sections were a notable pain in the neck. Sanding off
the stain in between the nooks and cranny's was quite labor intensive
and time consuming.
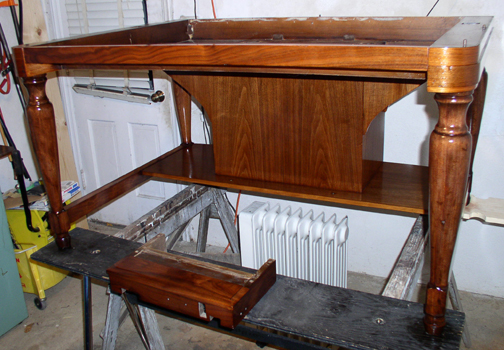
Multiple coats of finish
on all surfaces - 7 to be exact. This made me grateful
that I am an electronic tech and not a woodworker by trade - to
put it nicely.

The generator cover during
finishing - It turned out much better than I ever expected
considering it once looked like it went through a war.